Why do trains derail and how we can prevent it
Written by Chris, updated Jun 07 2019 in accordance with our editorial policy.
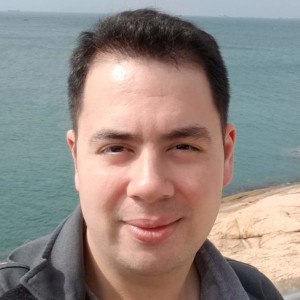
A study of 4 years of train derailment data shows trains most commonly derail due to problems with the track, such as broken rail. Other common causes are broken axles on the carriages caused by insufficient lubrication; weather events such as strong wind and flooding; and operator error such as allowing the train to run too fast. We’ve taken a look to find the underlying causes, and what jobs can be done to prevent train derailment.
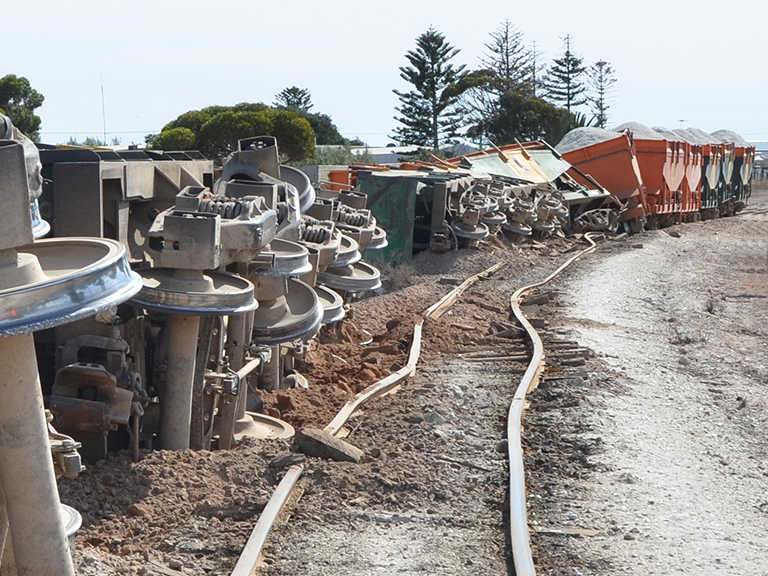
Thankfully there were no serious injuries or fatalities in the recorded derailments, a couple of drivers were shaken up though when their vehicles tipped over.
What causes train derailments
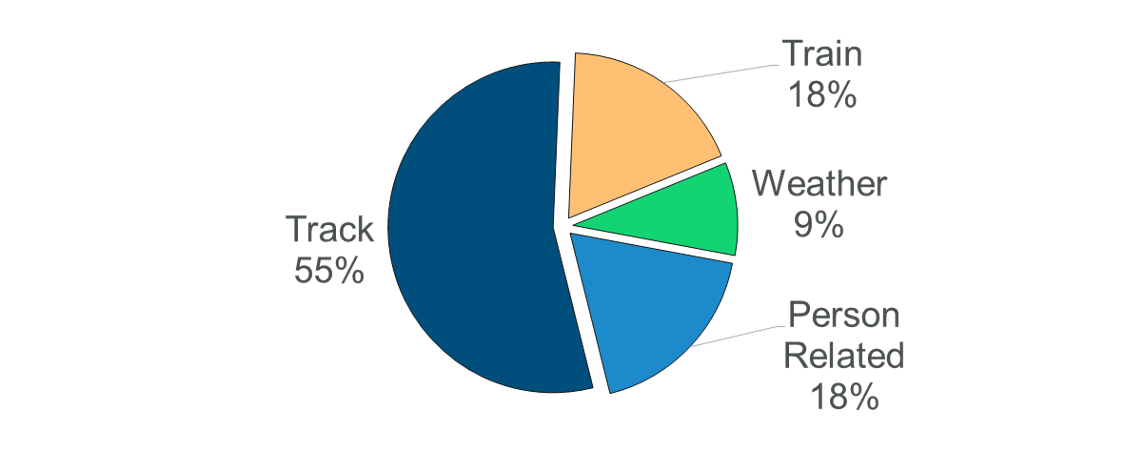
Track
Broken track is the number one most common cause of train derailments. Broken track is a catch all I’m using to describe a few different ways track can ‘break’:
- The distance between the two rails changes;
- Twists in the rail - when the rail transitions into a curve (think about the force you feel when you start turning in a car at speed).
- Cracks develop in the rail, it can even split into two pieces;
How does the difference between two rails change?
I found in the data two main causes of the distance between the rails changing: Track bunching and the bed the track sits on (ballast) moving.
As the train exerts force to move over the rails, the metal in the rails bunches backwards. This changes how the rail acts in the heat. In direct sunlight, even on a 30°C/86°F, the rails can get very hot. As the bunching has changed how the rail acts under heat, each rail may drift apart horizontally from its partner. When a heavy train runs over at speed, this difference between the rails may be enough to knock a wheel off the rail. The track may also buckle under heat.
Rain washes away the bits of rock and dirt (ballast) that the rails sit on. This makes them uneven. Sleepers (made of steel, wood, or concrete) try to hold the rail in place. As the ballast washes away, the rail held in place by sleepers no longer maintains its shape. This can make a rough ride for the train, occasionally rough enough to allow one of the wheels to come off the rail.
How do cracks develop in the rail?
The data tells me it’s mostly related to old joints, where the weld hasn’t stood the test of time.
Flash-butt welding was used to join the pieces of rail that broke in the source incidents. Older techniques for flash-butt welding may have allowed problems to develop in the quality of the weld. As the weld breaks down through use, cracks can start to form in the surrounding rail, or the two pieces of rail can separate. A train passing over this cracked or broken rail can consequently derail.
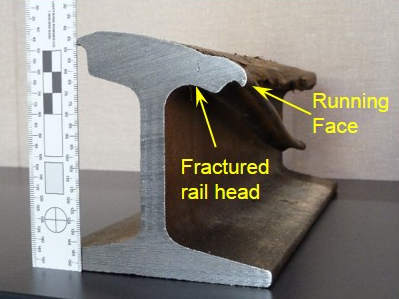
What about going around a curve?
I found a couple of cases where the train was going around a tight curve and derailed from the track.
This happens because the wheel climbs over the rail. Wheels are shaped to help them grip the rail. As they go around a curve, the wheel climbs up the rail. To prevent this from happening, you put grease on the wheels so they slide back down the rail (we’re talking about the inner part of the rail here, not the top). If there’s too much friction between the wheel and this inner part of the rail, the wheel will climb up too far and the train will derail.
Trains
Trains can derail themselves due mostly to broken axles and broken wheels.
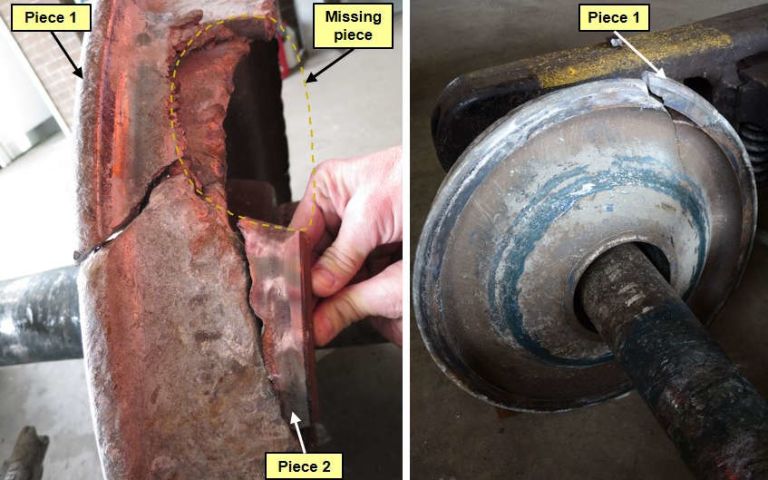
How do axles and wheels break? Heat.
If a rotating part gets stuck, or brushes against a part in a way it shouldn’t, it will get hot. As the rest of the heavy train forces this part along, it will get very hot. If it gets too hot it will break. A hot axle or hot wheel can break down, particularly if there are already cracks or other problems in the metal. Once that happens, the wheels can derail and take the train with it.
Weather
In the 4 year study period, weather caused 2 derailments.
Trains work great over long flat stretches of land; unfortunately so do floods. In one case, water flooded through the tracks after heavy rain and washed away the rocks and dirt (ballast) holding the tracks in place. Without ballast holding the tracks in place, the next train to go over those tracks fell off, even at its slow cautionary speed.
Imagine how tall a shipping container is. There are some train carriages which are taller. Along came an incredibly strong wind one day, and it blew over these tall containers. The train derailed.
How can we prevent trains derailing?
Fixing broken rail is the job of the Permanent Way Engineer.
Permanent Way Engineers inspect track to try to find evidence of these problems occurring, and fix it when they can. Inspecting the track might involve driving a special vehicle over the top analysing the track for problems, or it might be as simple as walking along and seeing if you can spot any issues. Fixing broken rail can include:
- Cutting out the broken piece and welding a new piece into place;
- Replacing the sleepers that hold the two rails at the correct distance apart;
- Cleaning and ‘fluffing’ the ballast to help it hold the rails in place;
- Making sure lubrication is applied to the right part of the track and wheel as the train passes through.
Fixing broken axles and broken wheels on a train is the job of the Rolling Stock Engineer.
Rolling Stock Engineers are responsible for keeping trains running. They figure out if there are any problems with the wheels and axles, as well as all the other air, oil, electric, and mechanical systems on the train. A suite of tools helps them with this job, such as sensors that alert engineers when train axles are getting too hot.
Rolling Stock Engineers typically…
- See if wheels and axles might break, and replace them when they’re showing signs of wear;
- Ensure moving parts of the train have the right amount of lubrication on them;
- Monitor the trains as they’re in service to predict wear that might occur, and determine the best time to replace those parts on the train.
I wrote recently about the different jobs you can do to keep a train network running smoothly. I believe Permanent Way Engineers and Rolling Stock Engineers have huge growth potential for jobs in the future. This is due to the number of rail projects that are being built at the moment. Click here to check out that article.
How often do trains derail?
I looked at 4 years of reports from a jurisdiction that requires reporting of derailments. This record included 22 derailments, or approximately 5.5 derailments per year over the tens of thousands of train travelled kilometres in the country. No one was seriously injured in this time, no one died. There was however costly damage to infrastructure that the maintenance engineers had to repair.
Train derailments are rare these days. Even when they do occur, its unlikely anyone will be seriously injured or die. Derailments may have an impact on cost though, through lost use of the line and money spent repairing the infrastructure. The right investments in maintenance, from equipment to staff, can help an operator prevent loss from derailment.
References
Photos and data used in compiling this article are extracted and derived from reports produced by the Australian Transport Safety Bureau (ATSB). Original reports produced by the ATSB can be found here. The study period was from October 2013 to November 2017.